с применением ренгеновского излучения
Контроль качества:
неразрушающий контроль паяных соединений
с применением ренгеновского излучения
В настоящее время в силу широкого использования BGA-,FBGA-,CSP-, и Flipchip-технологий соединений и сборки печатных узлов все более весомую значимость приобритает неразрушающий контроль качества паяных соединений с использованием рентгеновского излучения. Этот метод чрезвычайно актуален вследствии того, что инспекция потобного рода соединений другими методами (визуальными и прочими) крайне затруднена. В данной статье дан обзор опыта использования полуавтоматических компьютерных рентгеновских систем для контроля качества паяных соединений компонентов с подложкой. Обзор составлен на основе практического опыта компаний, предоставляющих услуги в области подобного сервисного обслуживания.
Компании, предоставляющие подобного рода сервисное обслуживание — инспекция с применением рентгеновских технологий, сталкиваются с большой, постоянно меняющейся номенклатурой изделий, а также с разными партиями продукции — от мелкосерийных до крупномасштабных. При этом охват оцениваемых качественных критериев может включать в себя разные варианты — от стандартного контроля качества до углубленного анализа причин возникновения дефектов. Эффективное и надежное решение задач контроля качества в данных условиях требует объективных исследовательских методов, современного рентгеновского оборудования и соответствующего программного обеспечения. Причем большие временные затраты на настройку программного обеспечения, контролирующего анализирующие и управляющие механизмы системы, представляют собой одну из основных проблем при инспекции мелкосерийных партий исследуемой продукции.
Требования и критерии контроля качества
Известен ряд основных дефектов, влияющих на общую функциональность печатного узла после BGA-пайки и требующих обнаружения: наличие перемычек (замыкания), отсутствие галтели, сдвиг, непропай.
Замыкания, отсутствие галтели и сдвиг могут быть определены уже при просмотре объекта инспекции на мониторе оператором, в тех случаях, когда излучение проводилось вертикально к объекту инспекции. В отличие от этих «грубых » дефектов, определение непропая требует, как правило, направления рентгеновских лучей под углом к объекту инспекции и высокого разрешения изображения. При этом могут быть определены пустоты непосредственно в паяном соединении, а по форме припоя можно определить недостаточную смачиваемость соединяемых поверхностей в большинстве случаев на стороне печатной платы. Из практического опыта следует, что обнаружение непропая таким методом (экспозиция под углом) является в настоящий момент преимущественным, по сравнению с другими методами рентгенотехнической инспекции (в частности, методами томографии), что и показало независимое исследование на PBGA с шагом выводов 1,5 мм [1,2 ]. Этот метод эффективнее в плане точности определения дефектов и экономичнее по затратам времени.
При исследовании паяных соединений, выполненных с меньшим шагом выводов, таких, как FBGA, CSP и Flipchip с использованием рентгеновского излучения, направленного под углом к объекту, из-за наклона объекта инспекции неизбежно возникает большое расстояние между исследуемым объектом и источником рентгеновского излучения. Что, в свою очередь, не позволяет достичь достаточно высокого разрешения изображения. Это препятствие может быть преодолено только путем применения специального технического оснащения рентгеновской системы, которое позволяет достичь высокого геометрического увеличения при излучении под углом к объекту инспекции (OVHM — Oblique View at Highest Magnification).
Для оценки надежности печатного узла необходимо также применение других исследовательских критериев. Так, важным параметром является качество смачиваемости соединяемых поверхностей. Соответствующий этому параметру контрольный критерий зависит от того, определяется ли зона смачиваемости контактной площадки самой металлической поверхностью контактной площадки или же нанесением защитной маски. Применительно к первому случаю, при условии хорошей смачиваемости контактных поверхностей припой как бы «оплывает » контактную площадку. На рентгеновском изображении становятся хорошо различимы темные кольцеобразные окружности по краям контактных площадок, градация цвета которых предопределяется толщиной припоя, как показано на рис.1.
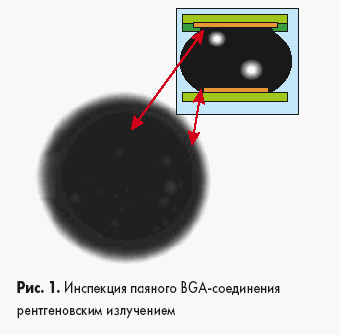
Относительно второго случая, характерным является то, что паяное соединение отображается в виде темных налегающих друг на друга окружностей. В этом случае излучение рентгеновских лучей под углом к исследуемому объекту при высоком разрешении (OHVM) дает возможность провести точный анализ смачиваемости соединяемых поверхностей.
Важной составляющей оценки степени надежности соединения является анализ паяных соединений на наличие пустот. Пустоты отображаются на рентгеновских изображениях в виде светлых окружностей внутри мест пайки (рис.1). Необходимость предоставления подобных высокоточных и детализированных изображений диктует очень жесткие требования ко всему комплексу рентгеновского оборудования. При проведении подобных инспекций необходимо в достаточной степени «просветить » паяные соединения, сильно отражающие излучение, и в то же время не допустить чрезмерного просвечивания слабоотражающей поверхности печатной платы. В противном случае, отображение диаметра галтели может быть существенно искажено. Это означает, что на практике рентгеновская система должна функционировать при высоком рентгеновском напряжении (от 120 до 130 кВ), низком токе (от 4 до 20 мкA) с маленьким фокусным пятном (<10 мкм).
Квантификация результатов исследований (сравнение полученных при исследовании данных с эталонными параметрами)
Помимо непосредственных исследований зависимости получаемых результатов от устанавливаемых при пайке параметров представляется необходимым внедрение соответствующей системы контроля качества изделий при их серийном производстве. Контроль качества задается в основном статистическими методами и требует соответствующего статистического измерения объективно заданных величин на наибольшем возможном количестве проб (в некоторых случаях до 100%). Таким образом, простое наличие пустот в паяных соединениях еще не является само по себе фактором, снижающим надежность соединения. Решающим фактором в данном случае является процентное содержание пустот в единичных паяных соединениях [3 ], которое, в свою очередь, зависит от регулируемых параметров процесса [4 ]. В силу вышесказанного, для точной проверки качества компонента необходимо проведение измерения объема пустот и дефектов по возможности всех паяных соединений компонентов схемы. Качественные показатели, которые могут быть надежно оценены автоматически при серийном производстве, приведены в таблице.
Таблица.Контрольные критерии для автоматической BGA инспекции
Контрольный критерий |
Ошибка |
наличие перемычек (замыканий) |
короткое замыкание |
смещение галтели |
сдвиг монтажного компонента |
отсутствие галтели |
разрыв |
отклонения диаметра окружностей паяных соединений от эталонных значений |
неправильное давление пасты, плохая смачиваемость припоем, наклон монтажного компонента |
неправильная форма галтели |
проблемы смачиваемости, наклон монтажного компонента |
отклонение градации цвета паяного соединения |
наклон монтажного компонента, непропай |
пустоты и превышение норм допуска для пустот |
недостаточная надежность |
Автоматическая оценка качества BGA-пайки может быть осуществлена достаточно эффективно и относительно просто путем сравнения набора полученных при измерении данных с эталоном. Таким образом, при необходимости можно произвести и полуавтоматическую 100%-ную сортировку.
Пример: ручная инспекция с автоматическим анализом
Как пример для осуществления контроля качества изделий мелкосерийного производства был проведен анализ дефектов BGA-пайки. При этом образцы двигались оператором под источником рентгеновского излучения с помощью джойстика. Соединения были исследованы с применением специализированного программного обеспечения. Для оценки стандартных паяных BGA-, FBGA-и CSP-соединений был применен режим самообучения программного обеспечения, в результате чего программа распознала BGA-пайку, правильный диаметр паяных соединений и градации серого цвета (яркость припоя) непосредственно в процессе анализа, соответственно, не потребовав дополнительных временных затрат на свою настройку. При этом были измерены и сравнены с эталоном все качественные показатели, приведенные в таблице. Превосходство самообучающейся системы при проведении указанной инспекции выразилось в том, что оператору не нужно было отслеживать точное позиционирование и увеличение изображения при перемещении опытных образцов, что значительно сэкономило время на проведение оценки качества. Кроме того, применение самообучающихся систем позволяет получить результаты, которые могут отчасти не зависеть от параметров рентгеновской установки, пока они не превышают предел, заданный в программу критериев оценки. Работа «обученной » системы продолжается до тех пор, пока, как минимум, 80% оцениваемых паяных соединений, соответствуют заданным для объекта допустимым критериям качества. Как показала практика, этот фактор соответствует в большинстве случаев одному типу исследуемого объекта. В противном случае, оценочные данные могут вводиться также и вручную, ориентируясь на эталоны с допустимыми дефектами паяных соединений. В этом случае программа предлагает оптимальные для ввода значения или эти значения могут быть выявлены путем применения вспомогательных измерительных функций программы. Таким образом, на настройку системы для объектов одного типа в среднем уходило около 10 минут, в то время как сама оценка длилась примерно 2 секунды. Это означает, что основное время инспекции затрачивается на ручные операции. Затрачиваемое время на полный автоматический анализ, например, одного PBGA 255 при оценке от 4 до 6 контрольных позиций компонента, составляет одну, максимум — две минуты.
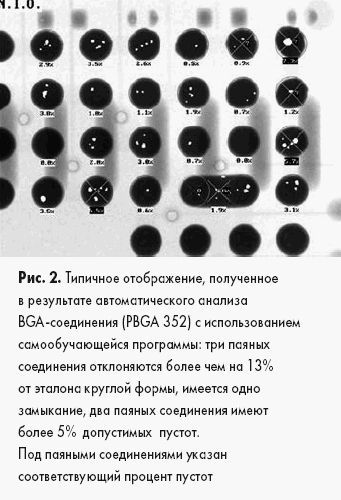
Рис.2 отображает результат инспекции BGA-пайки. Максимально допустимый процент пустот был установлен на уровне 5%. Надо отметить, что образования на задней стороне платы (припой с обратной стороны платы) хотя и ясно видны на изображениях, но при проведении анализа игнорируются, и, таким образом, никак не влияют на результаты оценки качества. При необходимости, для выяснения механизма происхождения дефекта, отклоняющиеся от нормы паяные соединения могут быть проанализированы в режиме OVHM (анализ с высоким разрешением под углом к объекту инспекции). Так, к примеру, на рис.3 показаны шесть паяных соединений одного µBGA-компонента. Здесь легко заметить легкий сдвиг галтели и различный диаметр паяных соединений. Также на помеченных соединениях была обнаружена недостаточная смачиваемость контактных поверхностей (нет темных колец, отсутствует плато). На OVHM-проекции (рис.4) подтвердилось то, что соединения действительно не пропаяны — припой висит лишь на «ножках » компонента. На паяном соединении справа внизу при вертикальной экспозиции можно еще увидеть характерное для данного соединения затемнение. Тем не менее, на OVHM-изображении по причине отсутствия так называемого «мениска » отчетливо заметно, что это соединение не пропаяно.
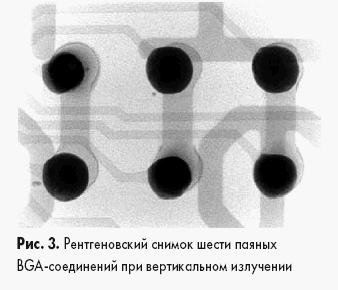
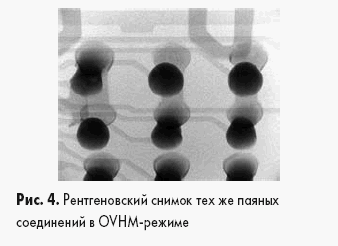
Автоматическая offline-инспекция (автоматическая инспекция в автономном режиме)
Для проверки крупных партий образцов, примерно от 20, имеет смысл применять автономную автоматическую инспекцию, при использовании которой образцы, после закрепления их в держателе (так же и стол или автоматическое устройство подачи), перемещаются и позиционируются автоматически. При этом также автоматически исследуются паяные соединения компонентов, попадающие в поле обзора датчиков системы. Результаты анализа записываются в соответствующий файл. При анализе BGA-компонентов со стандартным расположением соединений (полное заполнение рядов соединений), для облегчения процесса оценки в программе могут быть использованы предустановленные «библиотеки » BGA-компонентов. Единственное, что потребуется в этом случае сделать вручную, — это задать для обучения контрольные позиции компонента. При необходимости исследования компонента с нестандартным расположением соединений (например, при наличии одиночных не используемых монтажных соединений), позиции соединений могут быть введены вручную с помощью встроенного в программу интерфейса для каждого индивидуально. То же касается пороговых значений допусков и других параметров, включая настройки рентгеновской системы. Таким образом, контроль различных BGA-компонентов на печатной плате может быть осуществлен за один проход. На практике время настройки системы варьировалось для µBGA от 5 до 10 минут и, в зависимости от числа контрольных позиций, от 5 до 30 минут — для BGA, содержащего несколько сотен соединений. Время полного цикла проверки по всем критериям, указанным в таблице, варьировалось от нескольких секунд (для µBGA по двум контрольными позициями) до 2 минут (BGA 352 с оценкой 40 контрольных позиций).
Заключение
Накопленный опыт показывает, что благодаря минимизации времени на установку настройку системы, автоматический анализ квантификация паяных соединений компонентов с подложкой являются не только возможными, но и рентабельными даже для мелкосерийных партий исследуемых образцов. OVHM-метод (при размещении рентгеновского излучения под углом к объекту с высоким разрешением изображения) делает возможным произвести точный анализ также паяных соединений с малым шагом (CSP, Flipchip) и обнаружить неудовлетворительное смачивание соединяемых поверхностей. На настоящий момент остается актуальной автоматическая оценка смачиваемости соединений в OHVM-режиме. Но в силу огромного количества возможных видов дефектов, такого рода разработки требуют более глубоких исследований в области программирования алгоритмов анализа изображений.
Литература
- Вотинцев А., Медведев А. Выставка SMT/HYBRID/PACKAGING в Нюрнберге //Компоненты и технологии. 2002. № 8.
- M.Wickham. An Investigation into Ball Grid Array Inspection Techniques //ESA STM-261, сентябрь 1999.
- S.Liu and Y.H.Mei. Effects of Voids and Their Interactions on SMT Solder Joint Reliability // Soldering and Surface Mount Technology 18, 1994.
- W.B.O'Hara and N.-C Lee. How Voids Develop in BGA Solder Joints //SMT. 1996. Январь.
Станислав Борисенков, Александр Вотинцев, Хольгер Рот
|